Ultra-lightweight structures made in Luxembourg
26 January 2021
The Luxembourg Institute of Science and Technology (LIST) and the established Luxembourg company Gradel are joining forces by opening a joint Luxembourg Lab to research and produce ultra-lightweight structures for the aeronautics and space industry. Parts will be produced for three European giants in satellite construction; Thales Alenia Space (France), Airbus Defence and Space (France), and OHB (Germany). This project holds great promises for the space sector and beyond, with potential applications in the automotive and aeronautic world.
In the domain of space and satellites, weight is expensive. The heavier a product for transport into space is, the more it costs. In fact, the current estimate is costs of around €5,000-10,000 per kilogram, meaning that any weight loss is beneficial financially for companies sending satellites into space.
The LIST/Gradel joint effort aims to produce very tough, yet ultra-lightweight structures using continuous carbon-fibre-reinforced-polymers (CFRP) in a filament winding process creating ultralight 3D structures. The carbon fibre is coated with a polymer that solidifies the entire object rendering it extremely solid and resilient. Impregnated carbon fibres are wound to form an optimised 3D-mesh design that gives the part its special mechanical properties.
The joint lab, hosted in LIST’s new premises in Hautcharage, will focus on two projects, known as “xFKin3D” (the name of the technology) and “Robotised xFKin3D”.
While the first one consists of making parts by hand with the filament weaving manually and will target the demonstration space-use standards of structural parts produced by the xFKin3D technology, the second one aims at producing the same parts, but with the use of a new robotic arm recently installed at LIST. This will make it a fully automated manufacturing process, assuring excellent repeatability, to the same strength and quality, but on a larger, industrial scale.
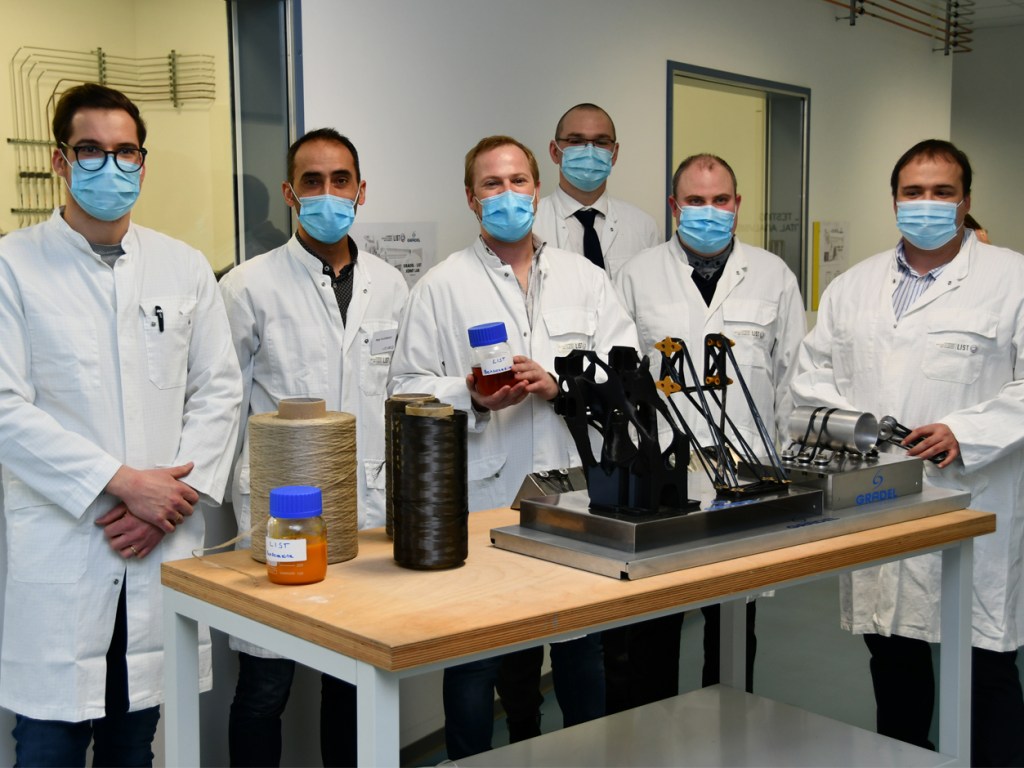
The end products are for aerospace, but what exactly?
The components produced are destined for use in all that is antenna support, bracket for equipment in satellites. Currently many of these parts are metallic and therefore relatively heavy. The aim is to move away from metal parts, and with this new technology by LIST and Gradel produced in Luxembourg, a reduction of up to 75% in weight can be achieved, saving companies considerable costs.
It has already been confirmed that the final clients for parts produced at LIST premises, will be initially for Airbus, Thales and OHB – three major European players in the space industry.
When it comes to commercialising parts produced in the LIST labs, it is Gradel who will take on this task with an already proven track record in producing products for the space industry.
LIST will contribute its expertise in the formation of the materials and play a major role at the start and of the process and development, researching and determining such things as the correct conditions, speed, printing, pressure, temperature etc, needed to obtain parts of strong and good quality.
“Setting up joint laboratory and development program to support innovative Luxembourg company is at the very heart of our LIST mission ” said Dr Damien Lenoble, director of the Materials Research and Technology – MRT Department of LIST adding that “advanced research towards ultra-light-weighting with sustainable materials and processes is one our CORE research area in MRT, acknowledging that targeting leading-edge requirements of the space industry together with GRADEL will pave the way for timely energy-efficient terrestrial applications that go from wind turbines to ultra-light transport vehicles”.
Regarding the new collaboration with LIST, Gradel’s Managing Director, Claude Maack stated, “Gradel began working with Ultra Lightweight structures in the space sector in 2018 by signing an exclusivity contract with AMC GmbH which developed xFK in 3D first in the Automotive sector. Now with LIST we have a strong partner with deep knowledge in material and process of composite structures allowing us further qualification for Space applications. Supported by LSA, this innovative process technology will enable Gradel to continue its success story in Space sector and beyond with a full automated manufacturing process”.
A disruptive technology with potential applications in the space field, and beyond
Light-weighting is a popular topic in today’s world, and becoming more and more important in many areas of production, notably in the automotive and aeronautic world. The heavier a car is, the more it consumes. If you manage to halve the weight of a vehicle, you halve the energy necessary to move it. This technology is currently being applied to space technologies, in the future it could equally be as beneficial for aircraft and automobile industries.
Both projects are supported by the Luxembourg National Space Programme LuxIMPULSE, which aims at providing funding to help companies established in Luxembourg to bring innovative ideas to market. The programme is managed by the Luxembourg Space Agency (LSA) together with the European Space Agency (ESA).